COMPOSITE PRODUCTION
Fiber™
Industrial-grade composites, featuring continuous carbon fiber and fiberglass tape for unrivaled part strength.
Offering users exceptional part quality and a wide range of aerospace and industrial-grade materials—all on a user-friendly, desktop printer.
Fiber™ is the only composite 3D printer to use Micro Automated Fiber Placement (μAFP™)—unlocking exceptional composite part strength for a desktop printer. Featuring closed loop heat control, the μAFP™ head constructs a high-density, continuous fiber reinforcement while the FFF printhead enables a high-resolution exterior shell.
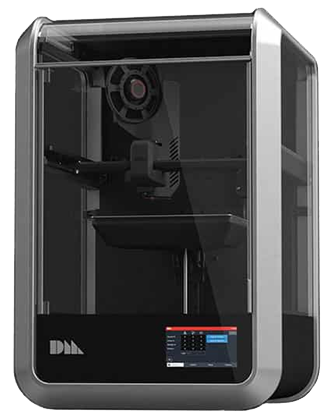
Technology | Micro Automated Fiber Placement (μAFP™) Fused filament fabrication |
Print system | CoreXY with robotic tool changer |
Build volume | FFF: 310 x 240 x 270 mm (12.2 x 9.4 x 10.6 in) μAFP™: 230 x 230 x 270 mm (9.0 x 9.0 x 10.6 in) |
Media | FFF Build media – Thermoplastic filament + chopped fiber Diameter 1.75mm μAFP™ Build media – Thermoplastic μAFP™ prepreg tape + continuous fiber, Width: 3mm |
Compatible Materials | Fiber™ LT – Nylon(PA6) +Carbon Fiber, Nylon(PA6) +Fiberglass Fiber™ HT – Nylon(PA6)+ Carbon Fiber, Nylon(PA6) +Fiberglass PEEK + Carbon Fiber, PEKK + Carbon Fiber |
Nozzle diameter | 0.40mm |
Onboard Controls | 7-inch touchscreen display |
Network Connectivity | Ethernet, USB |
Software | Fabricate® |
Print Sheet | Magnetically coupled, Flexible spring steel sheet, double sided, reusable. |